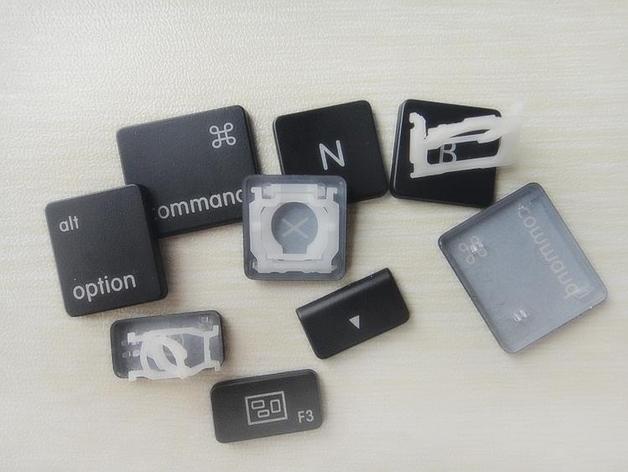
Assignment 10: "Creating New Industries" - Apple Keyboard Keycaps
thingiverse
This thing was made with Tinkercad. Edit it online https://www.tinkercad.com/things/0cWxqpHLv3k Use computer generated design data to create enclosures for Apple devices 3D printing can be quicker and less expensive than machining of prototype parts or production of cast or molded parts by conventional techniques (which can take from a few weeks to several months, depending on the complexity of the part) One application of 3D printing is production of parts such as enclosures for consumer electronics. Parts for consumer electronics may have small sizes, tight constraints on their dimensions and complex shapes, which can make traditional subtractive manufacturing method difficult or expensive. As a Technical Advisor in Apple’s Technical Support team, AppleCare, my job is to isolate the root cause of any issue a customer’s device is experiencing down to hardware or software; If the issue relates to software, I am expected to resolve the issue; If it relates to hardware, I am expected to refer the customer to an Apple Retail Store or Authorized Service Provider for hardware services. Most often, if the issue is isolated down to a fault with the hardware, the next question I am asked is how much we should expect the repair to cost. Of course, this is a complex question that requires a subjective answer mainly based upon: parts, availability of parts, and labor costs (which include validating and confirming the root of the issue as well as physically replacing any damaged components) At times, I have more technically savvy customers who have replaced components in their Apple Devices without the help of professional and are simply calling to inquire about how/where to purchase replacement components for their device. When I make a recommendation on where they should purchase these components, I always consider two main factors in my answer: affordability and reliability. If the components are available to purchase on Apple’s website, I will direct them there, but often times there are internal components like keycap replacements, Graphics Cards, Processors, etc. that we no longer offer online (especially for obsolete/vintage products.) In these cases, I generally try to locate the parts on a service provider’s website and refer them there. If Apple were to supply advisors in AppleCare and technicians in the Retail Division with a database of computer generated design data of replacement components for every Apple device manufactured, we could significantly cut repair costs and improve turn-around times for repair. I thought it could be gradually integrated into Apple’s repair process, starting small with some of the more common, minor hardware issues such as missing keyboard keys, home/side buttons for iOS devices, adaptors for notebook computers with missing ports, converters for traveling, stylus for touch screen devices EXAMPLE: For any missing keyboard key, searching by model number, obtain 3d printed design data for: the KeyCap : This is the piece of plastic that has the letter on it. the Hinge (retainer clip): The plastic or metal scissor clip pieces that hold the key cap to the base of the keyboard. (there are different Type clips for different models of Apple labtops) the Cup : This is the piece of rubber or plastic that acts as the spring to rebound the key after your press it. Getting a key replaced at the retail store or any service provider can run upwards of $60 for replacement parts and 85$ for labor. If you order these parts online from 3rd party providers, they often run around 3.95 – 5.95 per key, not including shipping costs. If these parts were at the hands of customers who are able to carry out their own DIY repairs and at the hands of technicians in store or in AppleCare, these parts could be printed quickly (reducing repair time) and at a much cheaper cost (avoiding shipping in replacement parts the store doesn’t have readily available), thus reducing repair costs and turn-around time for repairs overall. Because the type of material and the dimensions of the completed part must be consistent with the materials used to manufacture the original parts for that specific model, I think it would be most effective to supply these to technicians to reduce repair costs, but also to customers comfortable with doing a DIY repair, providing a simple process to generate the data for the part, and allowing them to either print the part themselves or have the file printed at a nearby service provider/retail store. If Apple were to provide these parts online, offering a repair service center components database in which the customer finds the correct model and 3d print files for their device by searching for their serial number will ensure that the correct replacement parts are printed every time. Custom Section What are BMGs? (Bulk Solidifying Amorphous Alloys) BMG = Bulk Metallic Glasses/Bulk-solidifying amorphous alloys (aka the technical term for Liquidmetal alloy) Recently developed class of metallic materials May be solidified and cooled at relatively slow rates At Room Temperature: retain amorphous, non-crystalline (i.e. glassy) stateAmorphous State: highly advantageous for certain applications (electronic components, medical devices, etc.) Solidification & Cooling Process for BMG Materials: amorphous state - produced by rapid cooling crystalline state - produced by slow cooling Risk of Partial Crystallization in the Solidification & Cooling Process: one risk with creation of bulk amorphous alloy parts is partial crystallization due to either slow cooling or impurities in the raw material; i.e. if cooling rate is not sufficiently high, crystals can form inside the alloy during the cooling process so that the benefits of the amorphous state are partially or completely lost (Source: Apple's Patent LAYER-BY-LAYER CONSTRUCTION WITH BULK METALLIC GLASSES http://www.google.com/patents/US20130309121) Limitations of Pre-existing Methods for Processing BMG Materials Developing Amorphous Alloy Systems Until the 90's, processability of BMG's was a lot more limited (amorphous alloys available in powder form or in very thin foils or strips with very small critical thickness (less than 100 micrometers)) Since the 90s more amorphous alloy systems developed based upon different elements with much lower critical cooling rates Since they have much lower critical cooling rates, they also have much larger critical casting thicknesses Shaping Amorphous Alloy Systems into Structural Components New Method using 3D Printing: New methods developed for casting BMG parts having a controlled amorphicity are needed (high degree of amorphicity and low degree of crystallinity) Apples Patent for Constructing a Part from BMG Powder (layer by layer) Using a layer of BMG powder capable of being fused to other layers through laser electron beam heating to arrive at the desired shape in an amorphous state suitable for internal and external components of electronics. (i.e. Keyboard Keys) Apple Inc.,. (2016). Layer-by-layer construction with bulk metallic glasses. United States. (http://www.google.com/patents/US20130309121)
With this file you will be able to print Assignment 10: "Creating New Industries" - Apple Keyboard Keycaps with your 3D printer. Click on the button and save the file on your computer to work, edit or customize your design. You can also find more 3D designs for printers on Assignment 10: "Creating New Industries" - Apple Keyboard Keycaps.