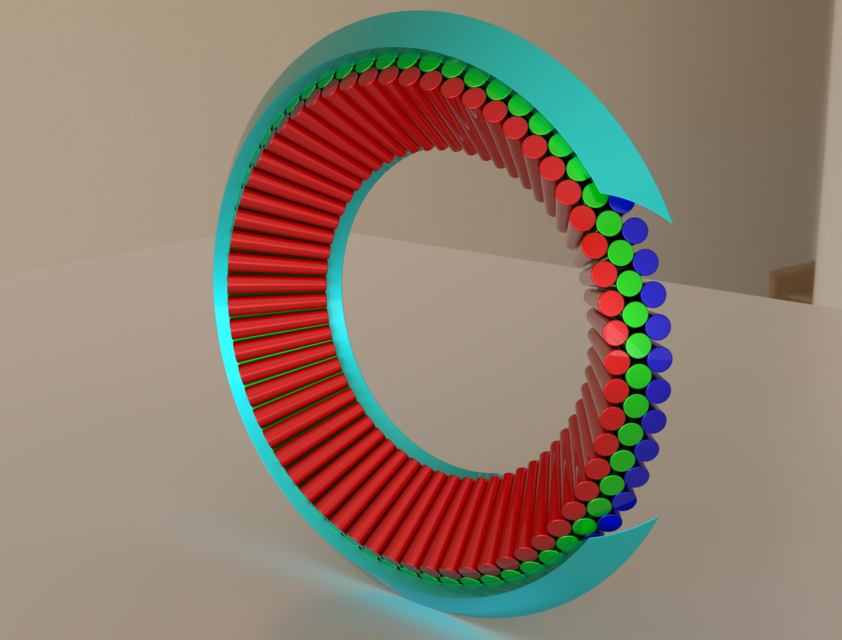
Cageless, Multilayered, Full Complement Radial-Axial Tapered Roller Bearing - design 03
grabcad
Similar to the 'Cageless, Multilayered, Full Complement Axial Roller Bearing - design 01' concept.The primary departure from that design lies in the bearing's rollers being substantially angled downwards (or viewed from another perspective, upwards) towards the center of the bearing so their rounded surfaces grasp a considerable component of both radial and axial forces the bearing endures, rather than only axial load.As with other bearing designs, three stacked layers of intermeshing, interspersed rolling elements are utilized instead of one single layer.The bearing's rollers are tapered, not uniform cylinders, and are arranged in a radial pattern so their respective axes of rotation converge to a common point in the middle of the bearing.The middle row of rollers maintains separation between any two consecutive rollers in either of the other two rows while reciprocally keeping its own elements apart with rollers from the other two layers.The middle row is load-bearing as well, transferring load between the other two.The rolling elements must be tapered cylinders or truncated cones since their axes of rotation are not parallel to the bearing's shaft axis.This means for each complete revolution, the ends of the rolling elements facing away from the center need to travel a longer distance than their opposite ends, which face towards the bearing's center. However, both ends of any individual roller must spin at the same RPM.Which necessitates that the diameter of the rollers be greater at their outward-facing ends than their inward-facing ends in direct proportion to the differing lengths of distance they must respectively travel for the bearing to complete one full revolution.As with other designs, this bearing should inherently adjust automatically for slight variations (owing to manufacturing tolerances) in the diameters of its various rolling elements as long as the ratio between endpoint diameters is preserved.It should also spread both axial and radial load evenly across all rollers due to their positioning into a stable arrangement under load.As with other designs, an even number of layers cannot be used because they would convey rotation from one bearing surface to another, defeating the purpose of the bearing and the use of rolling elements inside it.A single layer of rollers would be no different from tapered roller radial-axial bearings currently in widespread use which exhibit sliding contact either between consecutive rollers or have sliding contact with a cage that keeps them separated but which they all slide against contributing to friction heat and wear.
With this file you will be able to print Cageless, Multilayered, Full Complement Radial-Axial Tapered Roller Bearing - design 03 with your 3D printer. Click on the button and save the file on your computer to work, edit or customize your design. You can also find more 3D designs for printers on Cageless, Multilayered, Full Complement Radial-Axial Tapered Roller Bearing - design 03.