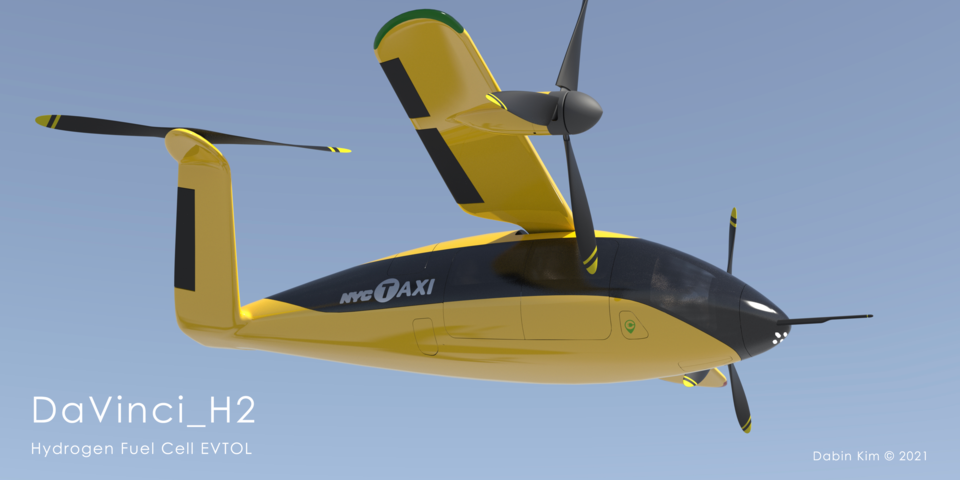
DaVinci H2
grabcad
After two weeks of planning, calculating and modeling, I present to you the DaVinci H2 : my hydrogen solution to the EVTOL/UAM race. Although battery tech is improving, it can only take us so far in aviation. Energy densities of lithium ion batteries have only increased twofold over the last 10 years, and battery lifespans suffer due to the energy-intensive vertical take-off/landing that current Urban Air Mobility solutions employ. Hydrogen, despite its current drawbacks (scarcity + high cost + relative lack of infrastructure) has several powerful advantages : high energy density, quick refueling, and ease of component replacement (it is much easier to replace a hydrogen tank/fuel cell than an EV battery, which is often a significant fraction of total vehicle mass). As such, I believe the UAM market will soon be dominated by hydrogen fuel cell aerial vehicles.About the DaVinci H2The DaVinci H2 is a harbinger for a hydrogen change; it combines the most optimal design elements of current EVTOL design proposals with the advantages of hydrogen. A tiltwing layout means that, unlike a tiltrotor aircraft, the wings begin to generate lift much sooner, which allows for a smoother and less power-intensive take off and landing. The lack of complex tiltrotor mechanisms ensures mechanical simplicity, leading to easier integration of system redundancy and less engineering and manufacturing challenges. The DaVinci H2 also uses distributed electric propulsion - a 48kWh floor-mounted battery can independently power the vehicle, or assist with power requirements during vertical ascent and descent, reducing the loads on both the battery and hydrogen fuel cell and increasing their service life. Although independently rechargeable via external outlet, the battery can also be recharged during flight with surplus fuel cell voltage. The current paradigm of UAM vehicles involves ground-based hubs, called vertiports. Adopting hydrogen for UAM means these vertiports themselves can serve as hydrogen refueling centers, not just for aircraft, but for road vehicles as well. With this, the introduction of hydrogen fuel cell propulsion to the UAM market will hopefully spearhead the mainstream adoption of hydrogen fuel cell technology, opening up a greener, more sustainable future.Hydrogen Fuel Cell System Power/Energy DensitiesTo derive a realistic prediction of a hydrogen fuel cell VTOL aircraft, I used the following publicly-available data. Note that, unlike a lot of proposed UAM designs that rely on projected battery energy densities of over 360wH/kg, this design relies mostly on the performance of extant systems :Tesla Model 3 Long Range : 78kWh / 1730kg / 440km rangeHyundai NEXO : 157L H2 / 1810kg / 600km rangeAssuming the same rolling resistance and drag coefficient for both vehicles, the NEXO’s 157L of H2 amounts to approximately 111kWh of energy. Considering the mass difference (80kg) and energy capacity difference (33kWh) of the two vehicles, it is already evident that hydrogen, even as a fuel cell system, offers superior energy density. The NEXO's fuel stack specifications are as follows : 3.1kW/L and 2.0kW/kg for power density. Its tank mass density (storable hydrogen mass as percentage of total tank mass) is 7.18%. Using this as a reference, a hypothetical 300L + 96L (auxillary tank for 45 minute flight reserve) hydrogen system will yield around 281kWh for 16kg of H2 for a total tank mass of approximately 224kg. Assuming a 420kW hydrogen fuel cell, the fuel cell mass will be approximately 210kg, and if accounting for ancillary systems such as pumps, temperature control units, filters, etc... we can assume a total mass of 350kg. The aforementioned 48kWh battery, using conservative Li-ion battery energy density figures of 160wH/kg, will weigh approximately 300kg. With the battery included, the combined hydrogen electric system mass will be 874kg, for a total 329kWh of energy. This is a higher figure than any other comparable 5-seater EVTOL within the 2000kg range.About the projectAs a designer with engineering experience, this was truly a test of what I could do on Solidworks. My intention was to hone my A-Class surfacing (G2 continuity) techniques and vehicle packaging abilities, and I think the end results speak for themselves. Thank you for taking your time to read through, and hope you enjoyed it!
With this file you will be able to print DaVinci H2 with your 3D printer. Click on the button and save the file on your computer to work, edit or customize your design. You can also find more 3D designs for printers on DaVinci H2.