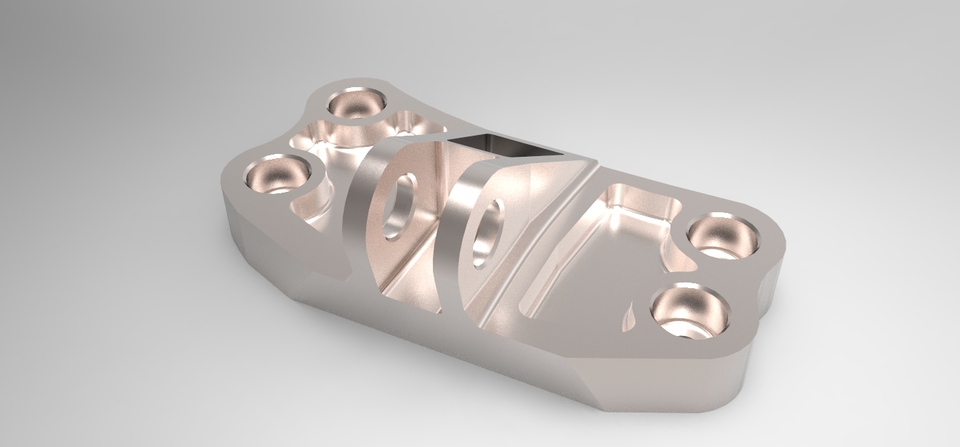
Engine bracket for GE™
grabcad
This proposed turbine meets General Electric's requirements, with a 50% mass reduction achieved through structural changes. Gradual thickness reductions (6 degrees) were implemented from the highest stress point to areas of less tension. Casting and machining processes also considered with a 5-degree tilt in cavities. The flange coupling pin has a gap of 4 for better structure, as it would be a slot in the part. Finite element simulations confirmed safety and efficiency. A reinforced bottom prevents buckling, and a gas outlet is included for pressure relief. Designed for machining or casting, with two-phase cutting using 3mm and 16mm cutters. Moment and shear forces were calculated to verify the part, and all slopes were revised accordingly. The turbine showcases excellent design and technical function support.
With this file you will be able to print Engine bracket for GE™ with your 3D printer. Click on the button and save the file on your computer to work, edit or customize your design. You can also find more 3D designs for printers on Engine bracket for GE™.