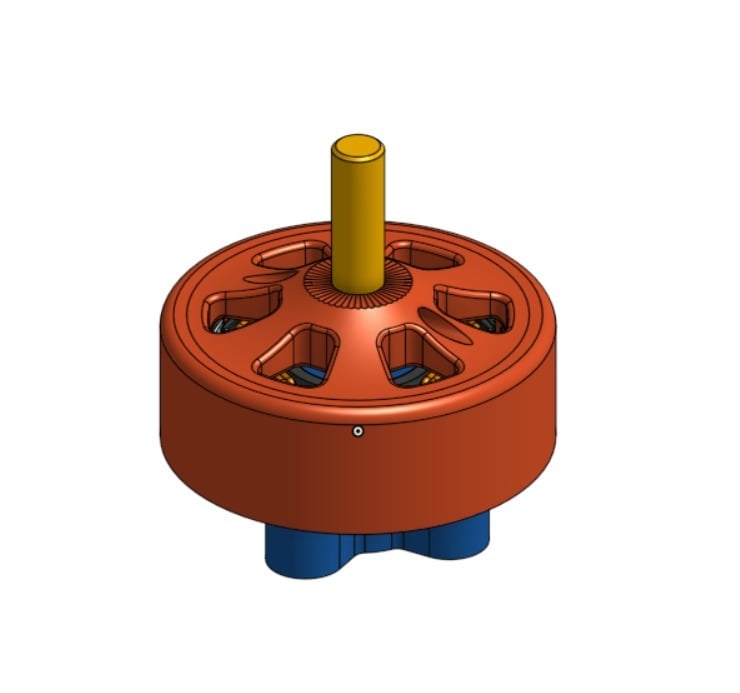
Experimental Brushless Outrunner Motor for RC Projects
thingiverse
**WARNING:** This is an experimental design. Be aware that no magnetic analysis has been conducted and the design has not been tested, so performance results are uncertain. The only guarantee I can make is that it will rotate. That's all. **Non-printable parts required** * 2 ball bearings measuring 8x4x3 mm. A minimum of 30,000 RPM rating is necessary, with a preference for metal caps on both sides to prevent dust accumulation. Metal cap designation is ZZ. * 12 neodymium block magnets measuring either 8x4x2 or 7x4x2 mm. Any heat-resistant class will suffice since the printed parts are the limiting factors. Opt for powerful magnets, with a good choice being anything in between N48-N52. For high-temperature resistance, look for designations like M or H at the end (e.g., N52H). * A half-threaded M4 bolt as a shaft. You can also use precision DIN pins and thread them yourself. Feel free to be creative and make it work with any standard M4 part. * 0.6 mm insulated winding wire, such as enameled copper or similar. * 2 M2 set screws. **Manufacturing** There are two different manufacturing methods that can be employed: * 3D print the entire thing. * 3D print parts as a master for epoxy/resin casting. For a quick but inefficient result, you can 3D print everything. If so, consider the following: * The stator core should be printed with a magnetic compound capable of withstanding high temperatures. Thinner layers may yield better results. * The bell should be sliced to maximize radial strength as centrifugal forces at high RPM will attempt to disassemble it. My 3D-printing-inexperienced recommendation would be to use: * Ferromagnetic-PLA for the stator core. This appears to be the only magnetic filament available, but it is not resistant to high temperatures. * Nylon or Polycarbonate for the housing, bell, and spacer. If you desire a stronger and potentially more efficient motor, consider using the 3D printed parts as a master to cast the production part in epoxy/resin. Keep in mind: * There exists a core production method called SMC (Soft-magnetic composite) that can be used to create the stator core from fine iron powder and high-temperature epoxy/resin. * The bell should be cast from a strong material, with analysis indicating that at least ABS-level tensile strength is required. Certain epoxies can provide this. **Assembly** * Wind the stator in dLRK combination with 7 turns per tooth (See [this](https://www.bavaria-direct.co.za/scheme/common/#prettyPhoto) for more details). * Glue the spacer to the inside of the housing and attach the bearings on each side. * Glue the stator to the housing. * Attach the magnets to the bell. * Place the shaft and the bell into the housing. * Use M2 set screws to constrain the bell to the shaft. **Links** For the CAD designs, click [here](https://cad.onshape.com/documents/1d82d48e1a626e89a966ae87/w/84fcab2a456c5856b1c34b16/e/3229e4f6269fb42a7bce95c6) For the bell analysis, click [here](https://www.simscale.com/projects/tapirath/2207_rc_brushless_motor_v1-2/)
With this file you will be able to print Experimental Brushless Outrunner Motor for RC Projects with your 3D printer. Click on the button and save the file on your computer to work, edit or customize your design. You can also find more 3D designs for printers on Experimental Brushless Outrunner Motor for RC Projects.