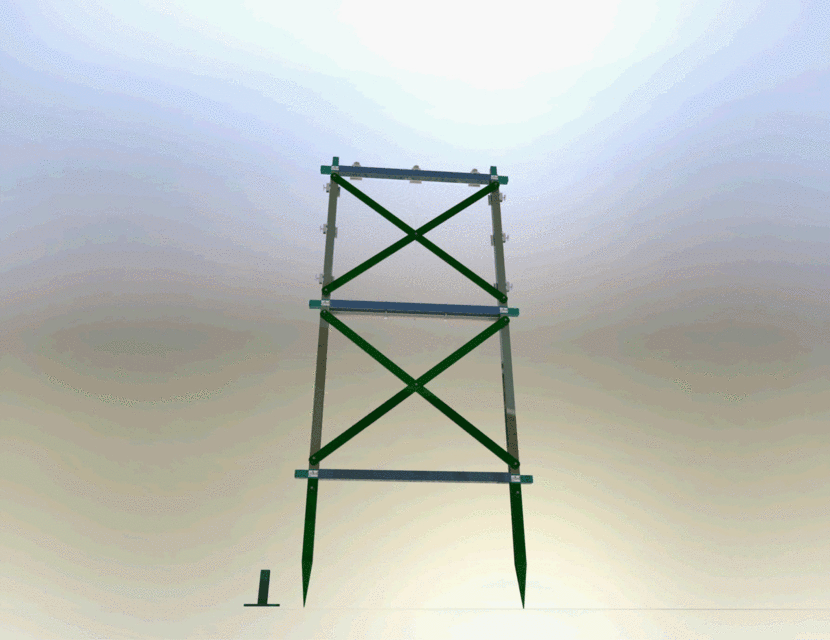
FOG NET TEST UNIT OF STONE
grabcad
Scalable Fog Net Test Unit - No Bolts, No Bird Bath, No Bull This design uses a minimum number of easily fabricated parts/part types (minimal fillets/chamfers). No screws, washers nor nuts to lose in the field. No screwdrivers nor wrenches to bring - just a spike plate, a sledge hammer and a level. Concrete is optional. Changing ground spike length to suit the unit's height/configuration, local ground rigidity and expected weather conditions can further reduce cost. Production of the assembly pins is achieved using basic drilling/shaping/forging. The mounting clips are a small 2 piece die cast part, with the addition of 4 springs, and some basic flat and round stock. For maximum strength, 50mm square steel tubing was selected, with a 4mm wall. For mass/weight/cost considerations, this could be changed to perhaps 40mm aluminum with a 3mm wall. Minimal setup currently comes to 100kg. 70mph winds are not a problem. Assembly pins use zero insertion force, with the exception of the two hangers, which are closely fitted and held in place by a small insertion force. Lock plates in the assembly pins are held in position (fully open or fully locked) by the coil/bearing inside. Tab on the end of the lock plate eases manipulation. Single unit design, for testing 1M^2 (Setup-1). Add another iteration on top for 2M^2 (Setup-2) and yet another for 3M^2 (Setup-3). Test multiple screen types, side by side, in the same horizontal array (Setup-4). The displayed screen is 0.25mm diameter at 10mm spacings, to minimize file size as well as for visual clarity. Setup-1 is in a .zip file in the /Files section. The rest of the files in the root folder are the contents of the Setup-1.zip file itself, with the images renamed. I will upload the larger screens and models, upon request. Construction and screen attachment is a breeze. Start by laying out the cross struts (small assembly pins pairing them up right at the start) and then the square tubing lengths on the ground, in formation, along with the vertical connectors. Snap those pieces together with long assembly pins, after you've properly placed your mounting clips (pull the knob on the clip's back side to slide over the holes to the correct position) on the square tubing. Two hangers , spaced evenly, are placed on the horizontal square tube that is situated at 1M above the ground. The water collector snaps into place, inside those two hangers. Once the main shape, all but the ground spikes, is assembled and laying flat and perpendicular to the install location, use the bottom vertical connectors as guides for ground spike spacing/placement. Once the spikes have been leveled and driven to the correct depth, the assembled frame can be brought to vertical by two people (3 people for Setup-3 or -4) and dropped on to the installed ground spikes. The completed frame is easily manipulated by gripping the unused vertical connector protrusions at the sides. The screen(s) can easily be installed during early phase of assembly, while still horizontal at ground level(laying thin slats across the frame to support the screen while fastening), or after the entire structure is fully built and in place, to save the screen from accidental contact during the lift. Precise tweaking of the horizontal tubing length, for the purpose of suiting standard screen roll width (if there is one), is easily done. Shown here is a screen width of precisely 1M, with heights of 1M, 2M and 3M, including the few mm of the bottom edge that is tucked just inside the teeth of the water collector. The water collector snaps into place, with the inward midbody force applied by the two hanger points on each wall helping to bring the top teeth sets of the collector slightly closer together (binding the base of the screen). Inside, the collector has a longitudinally centrally sloped bottom, to bring the water to the 6mm threaded exit (4mm inside), even if installed a little out of level. The exit is at the bottom centre, to minimize the water's length of travel/exposure to synthetics/tubing. A closed top to the collector and a small diameter collection point serve to minimize the evaporative loss. This also minimizes necessary maintenance/cleaning. The top of the water collector has a very narrow profile, with a centre-peaked top, to prevent contamination by wind-blown debris, insects, birds, etc. The screen mount clips are triple springed, for extra grip strength along the entire clip. The teeth are finely pointed and angled with a slight inward grab, to provide an aggressive hold. Once the teeth have a grip on the screen, incremental increase of screen tautness, point by point, is a snap. Makes for a quick screen install and/or replacement. 9 clips are shown on the simple setup, and 15 on the double height setup, but more or fewer can be easily used, based on maximum expected wind velocities (for example). Because the clips contact the square tubing on all 4 faces, they are installed by sliding them on to the end of the tubing before addition of the vertical connectors, cross struts and pins. A more complex (costly) version of the screen clip can easily be designed to resolve this condition of construction order. Also, the mounting clip's grab force could be further increased by using heavier springs or by converting the triple spring array to a single threaded clamp spindle with a knob to match existing. Personally, I would start with the shown version, for sake of cost. At a certain pressure threshold, strong winds will begin to tear the screen away from the teeth before they give way. But, when it comes right down to it, considering how effortlessly and quickly the screens are fastened with this design, it would make sense, working with this area/size of screen, when a wind storm is approaching, to merely take the screens inside and refasten them to the frame after the passing of the storm. For flow rate measurement, a small laser optical switch is installed in the gap at the top of each end of the collector box, just below the bottom edge of the screen's profile. Each water drop's fall from the screen's bottom edge will block/refract the light beam, coming from the transmitter box on the left side of the collector, and trip the switch inside the receiver box on the right, leading to a counter also inside the receiver box. Drip rate measurements can be tracked in a range of circuit-dependant ways. A rechargeable 9V battery in each box is enough to power the simplest iteration of the circuit. To further eliminate the labour of replacing batteries, a solar cell strapped to the top of a simple stake can be added, next to the unit - one for each box.
With this file you will be able to print FOG NET TEST UNIT OF STONE with your 3D printer. Click on the button and save the file on your computer to work, edit or customize your design. You can also find more 3D designs for printers on FOG NET TEST UNIT OF STONE.