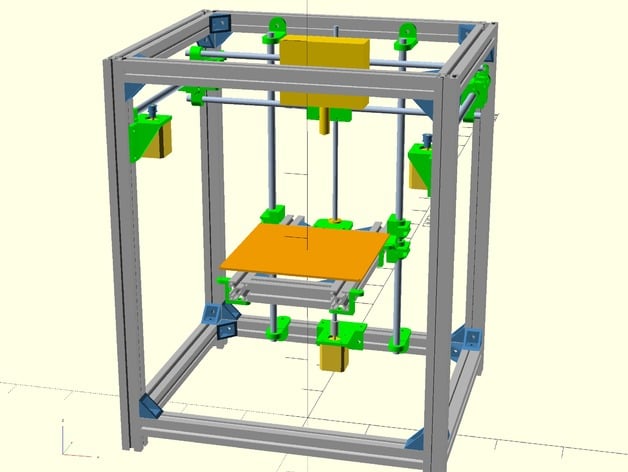
Fully Parametric 3D Printer CoreXY "HyperQbert"
thingiverse
It appears that you have provided a list of changes made to a 3D printing model over time. The changes are listed in chronological order, with the most recent updates at the end. Here is a summary of the changes: 1. **December 28, 2016**: Support for NEMA14 and NEMA23 motors was added. 2. **December 29, 2016**: Support for aluminum profiles 1515 and 4040 was added. 3. **January 11, 2017**: Fixes were made to ZBearingMount and YEndStopMount, and an extra strong version of the ZCarriage was added. 4. **January 12, 2017**: Screw slot holes were added to ZMotorMount, and a camera mount for Logitech C270 webcam was added. 5. **February 3, 2017**: A door magnet clamp holder was added, and the spool holder arms were lengthened. 6. **February 17, 2017**: Support for aluminum profile 2525 was added. 7. **April 8, 2017**: Optional X carriage extruder parts were added. 8. **September 11, 2017**: Fixes were made to the water-tightness of the XYMotorMounts. 9. **September 24, 2017**: The XYMotorMounts were made stronger. 10. **November 20, 2017**: Bugfixes and updates were made to various parts, including the addition of markings on carriage clamps. 11. **February 26, 2018**: Optional holder for LJ12A3-4-Z Proximity sensor was added, and support for bearing types LM8LUU, LM10LUU, and LM12LUU was added. 12. **October 10, 2018**: Optional hinge with screw as axle and XCarriage with cable hole were added. 13. **July 7, 2019**: The model was updated to take into account the length/width of hammernuts when calculating hole distance of XYIdler. 14. **August 31, 2019**: The model was updated to allow for a bigger distance between micro switch mount holes. 15. **September 8, 2019**: Bearings LM6UU and LM6LUU were added. These changes suggest that the 3D printing model has undergone significant updates over time to improve its functionality, strength, and compatibility with various components.
With this file you will be able to print Fully Parametric 3D Printer CoreXY "HyperQbert" with your 3D printer. Click on the button and save the file on your computer to work, edit or customize your design. You can also find more 3D designs for printers on Fully Parametric 3D Printer CoreXY "HyperQbert".