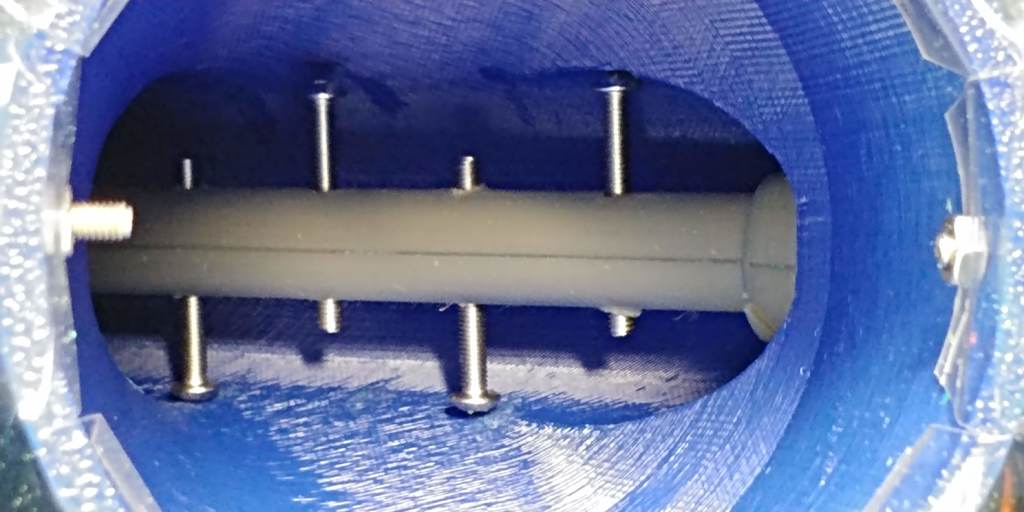
Revised Auger for Filastruder Auger Assisted Vertical Hopper
prusaprinters
<h3> ALERT!</h3> <p>This auger can be used with any version of the Auger Assisted Vertical Hopper (see Remix Source) parts, however, if you plan to use this auger, and have not already printed other hopper parts, printing the included bushing and hopper body will make your life measurably easier. Note that the hopper has channels to allow the screws in this auger to easily pass through, and the thread is reversed so that high torque does not unscrew the bushing. Consequently, the included bushing is required to mate with the reversed thread in the main body. Ideally, when using this auger, you are using the included hopper body and bushing models as well.</p> <h3> BACKGROUND</h3> <p>I prefer the vertical set up for efficient use of space, and because gravity becomes the pulling force to stretch out the hot filament, so a vertical hopper was the main option for my Filastruder. Recycled material, not being consistent in shape and size, would need assistance on it's way through the hopper and into the extruder. CNC Kitchen (YouTube) already showed that vibration is not enough to keep recycled scrap material moving into the extruder with this kind of arrangement. And so, the Auger Assisted Vertical Hopper by <a href="/universaljoint/designs">universaljoint</a> was a "no-brainer" solution.</p> <p>This is my third design after two previous revisions that didn't work so well. The first was not enough agitation and no movement at the bottom of the hopper, and the second was too much pressure. This iteration has a combination of those ideas, using pure agitation for the majority of the auger, but with a short amount of thread at the very end, right up near the Filastruder entry point, for the final push into the extruder auger.</p> <p>As you have probably already seen from the photographs, this auger uses screws through the shaft to agitate the material and half an auger thread at the end to make sure the material that gets that far is pushed into the Filastruder auger. In order to get the best, and most complete agitation of material by the screws, they must be nearly touching the inner wall of the hopper chamber, so as not to leave so much material hung up on the printed walls. The problem is, with the original hopper body, the auger won't fit into hopper if the screws are all the way out as far as they need to be. I've included an alternate hopper body to make this easier to assemble and service, but this auger can still be used if you printed another version of the hopper body. Here is the recommended process to be followed:</p> <h3> ASSEMBLY</h3> <p>IT IS RECOMMENDED that you print the included versions of the hopper main body and the auger bushing, instead of the originals. However, you can still use this auger with the original models, with a little extra work. You can also modify the original body by cutting into the threads to make channels. Refer to the hopper body model for my recommendation on where to put the channels.</p> <ol> <li>Print the auger model. PLA is fine. I used PETG.</li> <li>Assemble the two halves of the auger. Note that there are 2mm pin holes, one at the tip, and two at the base, to insert 1.75mm filament pins for easier alignment while gluing. Don't forget to install the square nut at the base before gluing!!</li> <li>Using M3 screws of sufficient length (M3x25mm is good, round or button head recommended), drive them into the holes that go all the way through the shaft. If you printed the included hopper body (ABS!), the screws need to be driven through so that the top of the screw head is 11.5mm from the surface of the shaft. A depth pin on a set of calipers is a good way to gauge it. The top of the head will be brushing the inside of the hopper body, so if it's too high, it will bind. If it's too low, you might have material stuck on the inside of the hopper. Alternating which side you drive them in is also recommended. </li> <li>Assemble the auger assembly, with the bushing and the large gear. A little bit of SuperLube (or similar) on the inside of the bushing, or the mating surface of the auger shaft, will make the system work nicely and with much less noise. Skip the next two steps if you printed the included hopper body.</li> <li>If you did not print my updated hopper main body, you'll need to drive each screw until it is about halfway through the shaft. The goal is to make it fit through the threaded auger opening in the hopper main body. If you don't drive them far enough through the auger shaft, you won't be able to fit them through the threads. Depending on the type of screw head and length of the screw, you might need to insert the screws into the auger shaft AFTER it's in the hopper main body, through the hopper opening.</li> <li>As you insert the auger into the hopper, use a long hex driver to UNSCREW the M3 screws, one at a time. Measure the distance between the top of the screw head and the surface of the auger shaft to be 11.5mm (less is ok, but more will cause binding problems) before moving to the next screw. Don't unscrew any of the next ones until you're confident that the ones you've already done are where you want them, because you'll have to screw them back in just to access a previously unscrewed screw. (LOL) Trust me, you'll figure this out quick. It was my idea, and I still had to mess around with each screw for a few minutes. Again, printing the included hopper body will make your life WAY easier.</li> <li>Fully install the auger by screwing the bushing into the hopper main body. In the end, every screw should be just touching, or slightly above, the inside of the auger chamber as it turns around. This is to help keep material moving down the shaft rather than sticking to the walls.</li> <li>Plug everything back together and get to extruding! And LMK if you run into any issues! PHOTOS</li> </ol> <hr/> <p>In case any of the photos are not self explanatory, here's what they show:</p> <ol> <li>Installed auger, looking into the hopper. You can see that the screws protrude through the other side of the shaft. That's a good thing. We don't want more places for plastic particles to get stuck, and more agitation isn't a bad thing. The important thing is that the screw heads are not pressed against the inside of the hopper chamber, but merely skimming it.</li> <li>Printed auger model</li> <li>Auger assembly with bushing and gear, ready to install. Note that the screws are pre-installed and set to the correct distance, for installation into the included hopper main body model with channels for the screw heads. If you're using this with an earlier hopper main body print, you'll need to install the screws as you insert the auger. I decided to go ahead and re-print the main body because it just makes this whole thing easier, not to mention cleaning and replacing things down the road.</li> <li>Print of revised hopper main body showing the channels for the screw heads to pass through the bushing threads.</li> <li>Inserting the auger with screws installed into the new main body. Easy peasy lemon squeezy! :)</li> <li>When using the original hopper main body, this is showing how I install the screws with a long hex driver. Remember, start with the one nearest the tip, and test each one before moving to the next one! You can avoid this fiddly step if you print the included hopper main body (and the bushing!) FILES</li> </ol> <hr/> <ol> <li>Hopper_Auger_Long_V2.stl - This is the operative part. It's in two parts in order for clean printing. With good elephant's foot compensation you should be able to print it, pull it off the plate, and assemble it with no trimming needed. Otherwise, remove any flashing.</li> <li>Filastruder_vertical_auger_assisted_hopper_V1_main_G4.stl - This is a new version of the hopper main body with slots on two sides of the thread for the auger bushing to make it easier to assemble the whole system. If you haven't already printed the main body, and intend to use this auger, this is the main body model you want to print. I wish I'd printed it. ;-) ABS is recommended. The threads for the bushing have been reversed to help make sure it stays screwed tight during use.</li> <li>Filastruder_vertical_auger_assisted_hopper_V1_auger_bushing_low-tolerance.stl - This is a revised bushing for the auger with a lower tolerance between the auger and the inner diameter of the bushing. This reduces the play in the auger, and can reduce (though not eliminate) the "crunching" of material in the hopper. A little bit of SuperLube (or similar) inside the bushing, or on the mating surface of the auger, will make this work nicely. This also has reversed threading, to match the reversed threading of the revised hopper main body. EPILOGUE</li> </ol> <hr/> <p>If you're not already a member, and you're working on your own filament extrusion system, even if it's not a Filastruder, PLEASE join our <a href="https://www.facebook.com/groups/963049850729874">3D Printer Filament Recycler Group on Facebook!</a></p> <p>Video of testing this version prior to successful extrusion run.<br/> <figure class="media"> <oembed url="https://youtu.be/vNp37S3AhYA"></oembed> </figure> </p> Category: 3D Printer Accessories
With this file you will be able to print Revised Auger for Filastruder Auger Assisted Vertical Hopper with your 3D printer. Click on the button and save the file on your computer to work, edit or customize your design. You can also find more 3D designs for printers on Revised Auger for Filastruder Auger Assisted Vertical Hopper.