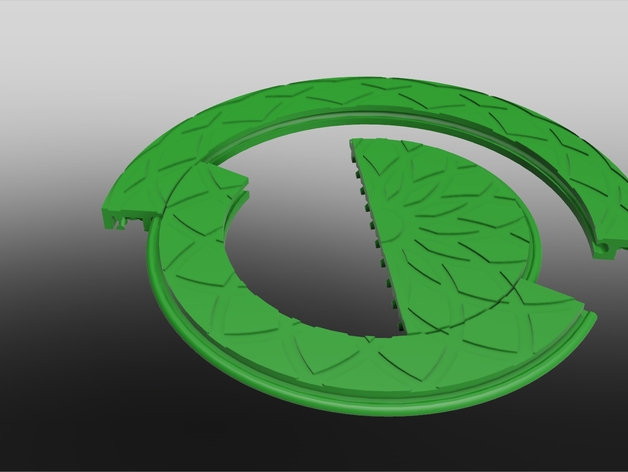
Rotating Trivet
thingiverse
Print with high-temperature filament only! It's a must to avoid failure. Adam Bujnowski, Alex Kinney, and Mark Traverso created this innovative trivet in their Virginia Tech Mechanical Engineering class for additive manufacturing. Eastman chemical supplied the prototyping material, and they based the design on their amphora line of filament, which is PETG-based. Colorfabb-XT and Taulman n-Vent are currently available as part of this line. Printing with amphora filament is highly recommended. This high-performance material has a higher melt temp than PLA or ABS, ensuring that the trivet functions perfectly. Although other PET-based filaments might work too, they haven't been tested yet. The trivet works seamlessly with most cookware at temperatures up to 110 degrees Celsius. To get the best results, avoid using high-temperature pans with this trivet. Doing so will cause it to melt eventually. Adam Bujnowski and his team cleverly designed the trivet based on the heat transfer properties of truss-based unit cell fins. It's crucial to print this design face-down, with the fins facing up when printing is complete. A heated bed provides excellent heat resistance in this orientation, helping the trivet withstand even the most demanding temperatures. If you try using an extremely hot pan with your trivet, be prepared for some nasty consequences. The print settings used were as follows: Printer Brand: Printrbot Printer: Simple Black Rafts: No Supports: Yes Resolution: 0.2 mm Infill: 30% PET-based filaments work incredibly well, and a honeycomb infill design provides optimal results. For the best print quality, make sure to use a minimum of three shells. If you decide to try out another material or filament, keep in mind that using a support with the sliding joint might be tricky to remove. I know from personal experience how frustrating it can be! A big thank you to Dr. Chris Williams for introducing us to the fascinating world of additive manufacturing through his fun and engaging classes. If you're thinking about taking ME 4644 or ME 5644, don't hesitate – do it! To Eastman Chemical Company, I'm deeply grateful for the opportunity to showcase a design featuring your high-quality product. You guys rock! Existing trivets often have basic designs that fail to optimize heat transfer and convection. They're also typically bulky and hard to store in the kitchen. By combining complex geometry with 3D printing, we created an innovative solution that tackles these issues head-on. We experimented with different materials until we found one that matched our requirements: high-temperature resistance and a wide range of customization options. After some intense research and comparison, Eastman Chemical Company's Amphora line caught our eye. Its exceptional melting and deflection temperature properties are ideal for this product. In fact, they outperform any other common 3D printing material by far! The availability of the Mass Portal extrusion printer sealed the deal. Now it was time to put theory into practice! We brainstormed many creative concepts but eventually narrowed it down to a semicircle design featuring a sliding joint that lets the trivet expand as needed. Underneath the pot, air channels are carefully cut out for efficient heat transfer via convection. And to disperse heat evenly across the underside, intricate fins have been added. When we were finished with our design, prototyping and testing followed closely. Using simulation software, we performed a thermal analysis that showed our trivet consistently operated 13 degrees Celsius lower than traditional models! But we didn't stop there – it was time to put our creation through its paces in the real world! Hot water pots and baking sheets were successfully placed on top with no adverse reactions. Unfortunately, things took a turn when we simulated a worst-case scenario: empty pans at maximum temperature caused severe warping, sticking to the counter, and complete melting. Based on this analysis, it's crucial that users limit their use of this trivet to boiling water pots, light cooking tasks, or baking-related uses where temperatures don't exceed 110°C. Trust us, we've seen the devastating effects firsthand! By using this trivet within these parameters, you'll enjoy unparalleled heat transfer performance without worrying about safety risks to yourself or your belongings.
With this file you will be able to print Rotating Trivet with your 3D printer. Click on the button and save the file on your computer to work, edit or customize your design. You can also find more 3D designs for printers on Rotating Trivet.