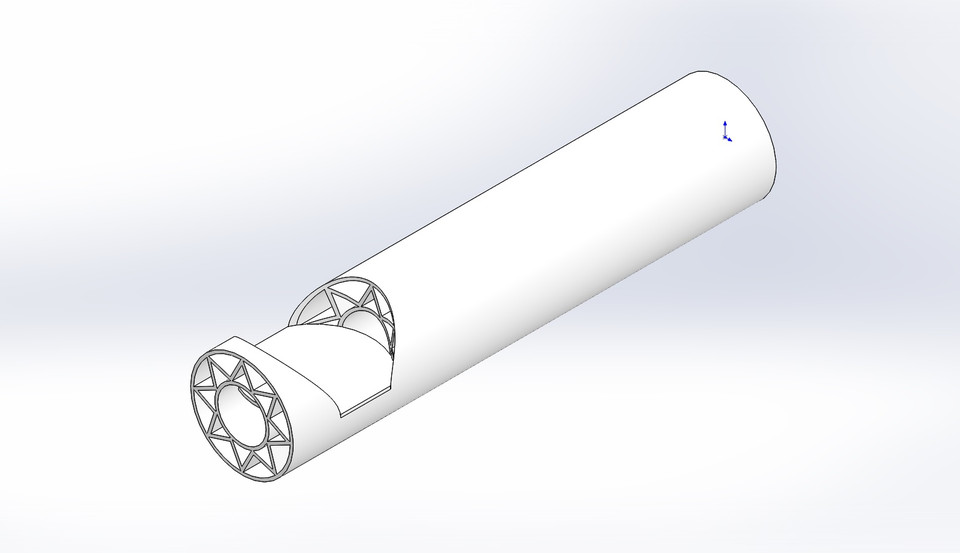
Structural Optimization of Drone Wing
grabcad
In my work, I developed an innovative wing design concept for drones that significantly outperforms the Fathom model. My design's honeycomb internal structure, made of ABS with a weight and length identical to Fathom's (21g, 127mm), reduced deflection by a staggering 1000 times under 50N downward force testing in Solidworks. While Fathom's wing deflected at 14.88mm, my redesign achieved an impressive .014mm deflection. To further optimize, I would identify the max allowable deflection and reduce size/weight accordingly for increased drone efficiency. This design concept can also be applied to other drone components like legs supports, offering lower drag due to its round shape. Manufacturing the honeycomb structure requires a 3D printer, adding complexity but improving performance.
With this file you will be able to print Structural Optimization of Drone Wing with your 3D printer. Click on the button and save the file on your computer to work, edit or customize your design. You can also find more 3D designs for printers on Structural Optimization of Drone Wing.